Blog
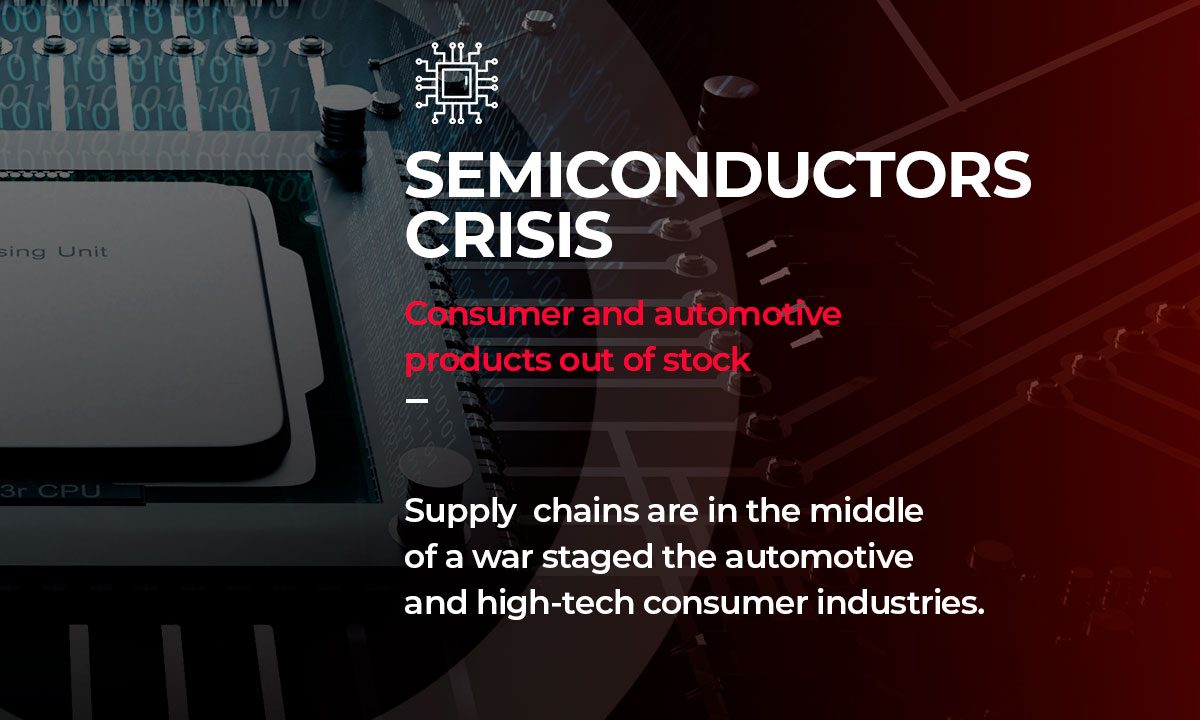
Posted on
20 September, 2021
in
Semiconductors’ crisis: The great supply chain disruption
When the new lifestyle triggered by the Covid-19 lockdown restrictions boosted the demand for consumer goods, it burst a crisis for microchips and other semiconductors, that now requires seamless logistics plans to keep factories working – and products available in many industries.
Specialized industries’ supply chains are facing one of the greatest global crises of the Technology Era: the war for semiconductors, conducted specially by the automotive and high-tech consumer industries.
The conflict’s great catalyst was the Covid-19 pandemic, which shut down auto plants while skyrocketed the global consumption of household electronics. But the problem’s origin is prior to the global lock-down.
The industry’s giant, despite having one of the largest manufacturing infrastructures and having one of the most appealing research and development funds in the sector, tried to become a mere foundry for other semiconductor companies.
Unfortunately, the effort failed.
Thus, while Intel struggled to deliver all the processors demanded by the market, the world underwent drastic cultural changes in the pandemic, such as the adoption of remote work, online education, and a boost in digital entertainment, generating a new tsunami of demand for semiconductors.
In 2020, Intel, Samsung and the South Korean SK hynix concentrated 33% of a market that sold 466 billion dollars in merchandise that year, according to an evaluation by the consulting firm Gartner.
On the other, we have those few giants concentrated in Asia – the first region in the world strongly impacted by urgent actions to control the spread of Covid-19.
With this, all the world production of electronics that use microchips was affected.
According to a study by McKinsey, in 2019 Automotive OEMs spent around 41 billion dollars in the purchase of semiconductors, but the pandemic depressed the market. Instead of growing around 6% compared to 2019 as expected, the sector’s demand contracted by almost 10%.
On the other hand, the demand for semiconductors for computers increased by 11%. Before the pandemic, the forecast for the sector was for zero growth.
In August 2021, nearly 20 auto plants in North America and Europe have stopped or reduced their production of vehicles and auto parts due to a lack of components, according to the Seraph consultancy.
Semiconductor shortages have affected auto manufactures in Michigan, Kentucky and Kansas (in the United States), Mexico and Germany.
Regarding a probable deadline for the crisis, while Ford CFO John Lawler told investors that he sees the microchip problem spreading into early 2022 and Ford’s president in South America, Daniel Justo, said the crisis is diminishing as some bottlenecks are being solved, although it may enter 2022, Intel leader Pat Gelsinger goes further and predicts he can see it extending across the next year, once demand vastly outstrips supply.
A chip can take three months and 700 processes to be manufactured. Any failure generates a butterfly effect that illustrates well the current crisis. In addition, it is important to have a comprehensive vision of the needs of a production, since other materials, such as steel and plastic, are also at risk of disappearing from the market due to global production and distribution problems.
Taking a long-term comprehensive view of inputs needs to a strategic plan, Toyota has been largely unscathed by the global shortage of semiconductors, before getting hit by the crisis – nevertheless, a few months after most of their competitor OEMs.
After the triple-disaster in 2011, the Japanese carmaker came up with a business continuity plan (BCP) that required suppliers to stockpile anywhere from two to six months’ worth of chips for this OEM, depending on the time it takes from order to delivery.
From an initial advisory session, we start to learn your most specific requirements, develop a diagnosis, and offer “white glove” service options: extremely sensitive to your delivery times and to the high value of your cargo, providing you total visibility and uninterrupted support.
An example of one of our clients’ success stories was having our hand carry service transporting, safely and in timely, semiconductors from Malaysia to Mexico.
In addition to Asia, for scheduled or urgent cargo, we are specialized in inbound and outbound solutions from and to all the Americas and Europe, mainly with premium air services, but also with the ability to design multimodal plans tailored to your needs.
If the semiconductor and microchip crisis extends into the first –or even last– months of 2022, we will equally work hand in hand you to keep your supply chain moving. Contact us today.
* We are EP America, a company of Europartners Group, your best strategic partner in logistics.

Specialized industries’ supply chains are facing one of the greatest global crises of the Technology Era: the war for semiconductors, conducted specially by the automotive and high-tech consumer industries.
The conflict’s great catalyst was the Covid-19 pandemic, which shut down auto plants while skyrocketed the global consumption of household electronics. But the problem’s origin is prior to the global lock-down.
The inception of the crisis is prior to the pandemic
Analyzing the market before 2020, we can see that the crisis was not born as a result of the pandemic: Intel, one of the leaders among microchip manufacturers, was revealing signs of problems supplying processors due to changes in its process of manufacturing since 2019.The industry’s giant, despite having one of the largest manufacturing infrastructures and having one of the most appealing research and development funds in the sector, tried to become a mere foundry for other semiconductor companies.
Unfortunately, the effort failed.
Thus, while Intel struggled to deliver all the processors demanded by the market, the world underwent drastic cultural changes in the pandemic, such as the adoption of remote work, online education, and a boost in digital entertainment, generating a new tsunami of demand for semiconductors.
The heart of the problem:
market concentration
So, on the one hand, we have the market distribution of the microchips and other semiconductor industry – it is extremely concentrated in a few large manufacturers.In 2020, Intel, Samsung and the South Korean SK hynix concentrated 33% of a market that sold 466 billion dollars in merchandise that year, according to an evaluation by the consulting firm Gartner.
On the other, we have those few giants concentrated in Asia – the first region in the world strongly impacted by urgent actions to control the spread of Covid-19.
With this, all the world production of electronics that use microchips was affected.
The consulting firm Deloitte estimates that 60% of all the microchips are manufactured in Asia, mainly in South Korea and Taiwan – country of origin of the Taiwan Semiconductor Manufacturing Company (TSMC), the giant in the sector.
According to data from one of TM Lombard economists, Rory Green, the two Asian nations are responsible for 83% of the world production of processor microchips and 70% of memory chips.
The conflict with the automotive sector
With automotive plants closed in the first months of the pandemic, semiconductor production was able to focus on meeting the new consumer electronics demand – for some time.According to a study by McKinsey, in 2019 Automotive OEMs spent around 41 billion dollars in the purchase of semiconductors, but the pandemic depressed the market. Instead of growing around 6% compared to 2019 as expected, the sector’s demand contracted by almost 10%.
On the other hand, the demand for semiconductors for computers increased by 11%. Before the pandemic, the forecast for the sector was for zero growth.
The automotive sector and the semiconductors
- A car can carry 100 electronic components and between 20 to 40 microcontrollers – that represents 35% of the cost of the vehicle.
- The automotive industry consumes around 10% of all the microchips sold in the world.
- Europe consumes almost 40% of the semiconductor supply.
- The crisis may grow more with the increase in demand for electric vehicles.
- The German automotive industry faces the worst semiconductor supply shortage in 30 years.
- More than 80% of the companies in the sector were affected.
- Hit hard by the lack of semiconductors, Mexico’s manufacturing experienced a 27% drop in July 2021 compared to July 2020 (the rise of the pandemic).
- The most affected production lines were those linked to light trucks (pick-ups) and utility vehicles.
“On the one hand, vehicle manufacturers are facing great challenges with sourcing and the supply chain of microchips for their current production. At the same time, they must accelerate designing ideas for their future models to reduce the number of chips used in each unit and to increase the necessary technology advancements to lead the markets of ‘tomorrow’.
The development of increasingly electronic, more interactive, more environmentally friendly and smarter vehicles is incessant.
While we recognize that large tier companies in the sector are committed to investing and producing more resources to support the supply chains of various OEMs, we know that higher production lines will remain under pressure throughout 2021 and 2022, causing ongoing ‘stress’ in distribution channels, to sustain competitiveness among OEMs.
Thus, just-in-time logistics solutions, urgent and other types of service focused on delivering in the correct time required by automotive customers will be inevitable in the planning of each supplier”.
Crisis can go beyond 2022
As Alexander Katsouris mentioned, the semiconductor distribution problem may extend all through the next year.In August 2021, nearly 20 auto plants in North America and Europe have stopped or reduced their production of vehicles and auto parts due to a lack of components, according to the Seraph consultancy.
Semiconductor shortages have affected auto manufactures in Michigan, Kentucky and Kansas (in the United States), Mexico and Germany.
“In one hand, German still relies a lot on locally produced inputs, and works close to Asian markets”, comments Rouven Blau, Europartners Group* German routes development manager.
“We cannot ignore the critical raw material supply chain situation, since it is endangering the companies’ development in technology”, he remembers, “but in other hand, one of the biggest Tier 1 companies in the country, Robert Bosch, has already determined their future development on the semiconductor chip market.
I think other companies will follow them, seeking to be more independent to secure their customers’ supply chains. Maybe soon we will see strategic alliances of companies, sectors or countries”, Rouven foresees.
Regarding a probable deadline for the crisis, while Ford CFO John Lawler told investors that he sees the microchip problem spreading into early 2022 and Ford’s president in South America, Daniel Justo, said the crisis is diminishing as some bottlenecks are being solved, although it may enter 2022, Intel leader Pat Gelsinger goes further and predicts he can see it extending across the next year, once demand vastly outstrips supply.
Common problem of industries that use semiconductors: mismanagement of stock
The explosion of demand by the consumer electronics and automotive industries, coupled with another parallel crisis –that of ocean freight – disclosed some failures:- in the production chains, completely unprepared for a forecast change of this magnitude,
- in the consolidation and management of emergency stocks.
A chip can take three months and 700 processes to be manufactured. Any failure generates a butterfly effect that illustrates well the current crisis. In addition, it is important to have a comprehensive vision of the needs of a production, since other materials, such as steel and plastic, are also at risk of disappearing from the market due to global production and distribution problems.
Taking a long-term comprehensive view of inputs needs to a strategic plan, Toyota has been largely unscathed by the global shortage of semiconductors, before getting hit by the crisis – nevertheless, a few months after most of their competitor OEMs.
After the triple-disaster in 2011, the Japanese carmaker came up with a business continuity plan (BCP) that required suppliers to stockpile anywhere from two to six months’ worth of chips for this OEM, depending on the time it takes from order to delivery.
An strategic partner in logistics
can take you through the semiconductor crisis
Relying on a strategic partner in logistics, such as EP America, gives you the possibility of having at hand a solid portfolio of premium services that can be combined to build a plan tailored to your needs.From an initial advisory session, we start to learn your most specific requirements, develop a diagnosis, and offer “white glove” service options: extremely sensitive to your delivery times and to the high value of your cargo, providing you total visibility and uninterrupted support.
An example of one of our clients’ success stories was having our hand carry service transporting, safely and in timely, semiconductors from Malaysia to Mexico.
In addition to Asia, for scheduled or urgent cargo, we are specialized in inbound and outbound solutions from and to all the Americas and Europe, mainly with premium air services, but also with the ability to design multimodal plans tailored to your needs.
If the semiconductor and microchip crisis extends into the first –or even last– months of 2022, we will equally work hand in hand you to keep your supply chain moving. Contact us today.
* We are EP America, a company of Europartners Group, your best strategic partner in logistics.

Tags: EP Air
Related posts
18 October, 2022
Machinery transportation using an air charter: a premium solution to avoid line stoppages
The peak season is here, and the holiday season is right next door. Only hand in hand with a strategic [...]
Read more20 September, 2022
What is an air freight consolidation service?
EP America’s Air Freight experts explain how the service works and its main benefits for your logistics plans.
Read more28 April, 2022
Aviation logistics: up and down to the last detail
To overcome an AOG situation, aviation logistics experts must act fast. Any detail missing can increase the [...]
Read more19 April, 2022
Aircraft engine logistics: a passion
To move aircraft engines between Texas (USA) and Sao Paulo (Brazil), you need a strategic partner in [...]
Read more